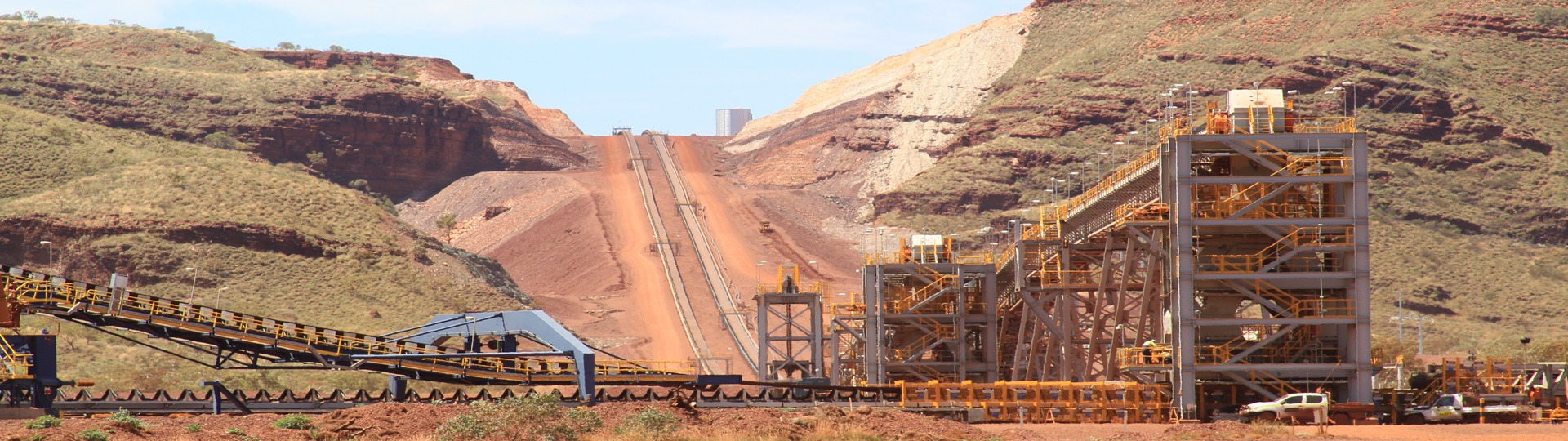
Overland Conveyors
OVERLAND CONVEYOR SOLUTIONS FOR MINING MATERIALS HANDLING
TNT’s custom overland conveyor systems deliver safer and more cost-effective solutions for transporting bulk materials on mine sites with less impact on the environment.
As the mining industry turns to more sustainable practices, TNT is partnering with mine operators to transition to overland conveyors for long-distance transport of crushed ores, waste materials and filtered tailings. Our systems help achieve significant operational savings while improving safety and efficiencies over the total life of mine compared to other modes of transport.
In rough terrain and challenging mining environments, overland conveyors can often be routed in a more direct path, reducing transport distance and eliminating the cost of an empty truck return haul.
By replacing trucks with overland conveyors, labor, training, fleet maintenance and energy costs are substantially reduced. Fewer truck movements are also better for the environment, decreasing fossil fuel use and CO2 emissions onsite.
Unrivalled global experience and know-how to meet any challenge
TNT has designed and delivered overland conveyor systems worldwide, typically integrated into our high-capacity crush convey systems, heap leach stacking applications or filtered dry stack tailings facilities.
We have provided a wide range of overland conveyor solutions with belt widths up to 84” wide and capacities of more than 15,000 tonnes per hour.
Our solutions have included a multitude of bulk materials and complex requirements such as horizontal curves, compound horizontal and vertical curves, downhill regenerative conditions, extreme temperatures, high altitudes and complex braking dynamics.
With extensive in-house expertise, we can engineer, design and install the right overland conveyor configuration for virtually any mining application.
KEY BENEFITS OF TNT’S OVERLAND CONVEYORS
Safe and Reliable
Unmatched system reliability with state-of-the-art drives and control systems, active take-up systems, dynamic braking and sophisticated on-board safety switches and sensors.
Efficient Operation
Technologically advanced condition monitoring equipment used for preventative maintenance, keeping your system operating efficiently for longer.
High Capacity
Conveyors can be built to transport up to 20,000 tonnes per hour, with significant lifts or declines over long distances with variable terrain.
Environmentally Friendly
Use less energy than haul trucks while significantly reducing noise pollution, dust pollution and water consumption for dust control.
Lower Emissions
Replacing diesel powered haul trucks with overland conveyors reduces overall carbon emissions. Downhill regenerative conveyors generate electrical power, producing clean energy.
One Stop Solution
Turn-key crushing, conveying and stacking solutions with design, installation, commissioning and maintenance capabilities under one roof.
Modularised Design
Systems designed for cost-effective modular construction, leading to quicker build times and reduced labor requirements.
IN-HOUSE ENGINEERING EXPERTISE
TNT has delivered overland conveyor systems worldwide in some of the most challenging terrains for a range of bulk materials – including crushed ore, acid laden agglomerated ores, dry tailings and waste rock.
Our in-house engineering team design customised systems using the latest technology and tools to deliver a robust solution that meets your conveying challenges.
We bring exceptional experience and practical knowledge to optimize your overland conveying system, with the ability to effectively design belt class, pulley sizes, idler spacing, drive configurations, take up types and standardization of components.
OVERLAND CONVEYOR KEY FEATURES
-
Dynamic Analysis
Long and complex conveyors are sensitive to dynamic conditions such as acceleration and deceleration, emergency stops, regeneration and, in the case of overland tripper conveyors, variable load and inertia conditions.
Our expert team carefully analyses all dynamic conditions – including starting, aborted start, operation stop and emergency step – to mitigate risk. This will ensure the appropriate drive, braking, electrical and mechanical systems are properly integrated for the safe, reliable and long-term operation of your overland conveyor system.
-
Discrete Element Method Modelling
By undertaking Discrete Element Method (DEM) material flow modelling we analyse how bulk materials move through transfer points and interact with the conveyor belt to optimize throughput, chute design, reliability and ultimately the overall performance of your overland conveyor system. This method is effective in identifying material build-up, blockages and wear to ensure proper material flow, so we can design your conveyor system to operate with greater efficiency for longer, with less downtime.
-
Horizontal, Vertical and Compound Curve Design
We can design overland conveyor systems with compound horizontal and vertical curves to solve complex challenges associated with transporting bulk materials in variable terrains.
Flexible conveyor configurations with optimized curves can greatly reduce earthworks, civil, structural and site installation CAPEX requirements. These curved overland conveyor solutions can also eliminate the need for maintenance intensive transfer stations by reducing the additional number of conveyor segments by aligning the conveyor design with the terrain.
-
Variable Speed Drives
Our overland conveyor systems use the latest state of the art drive systems with Variable Frequency Drive (VFD) speed control, dynamic/proportional braking and condition monitoring technologies.
-
Ancillary Devices
We carefully select and integrate a range of ancillary devices to meet the needs of your project, including longline onboard safety systems, smart monitoring, belt scales, metal detectors, cleaning systems and magnets to protect people and equipment.
-
Overland Tripper Systems
Overland tripper conveyors are often supplied as part of our mobile stacking systems, to ensure a seamless, integrated material handling solution from plant to heap leach pad, dry tails facility or waster stacking areas. Designs consider high overland conveyor belt tensions, mobility, alignment and belt lift.
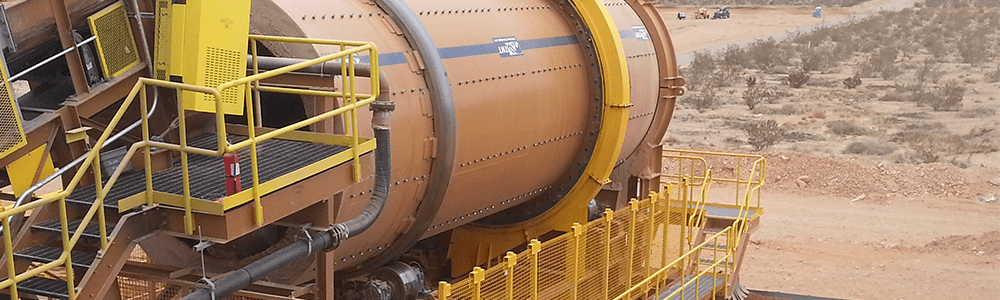
TALK TO US
Talk to us about your project.